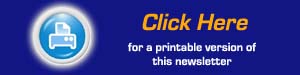
|
|
|
|

|
|






|
|
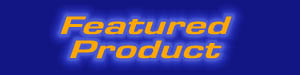
|
|
050-0810
Single Rotor Latch/Logic System
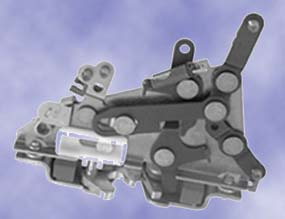
The 050-0810 Single Rotor Latch/Logic System is intended for occupant or
exit/entry doors for specialty vehicles including ambulance, fire/rescue
and off-highway vehicles (light duty) that require compliance to FMVSS 206
standards. The flexible design allows for internal or external door
mounting and provides automotive logic function with remote activating
handles. Other product benefits include:
- Floating
external paddle when locked
- Compatible
for the addition of power actuation and keyless entry
- Overrides
locking function with internal handle actuation
- Prevents
inadvertent lockouts
Other components are available and include
handles, latches, rods, brackets and powerlock actuators to provide a
comprehensive electro-mechanical access solution and comply with FMVSS 206
requirements.
050-0100 Two Rotor Latch
Withstanding the
test of time and severe applications, this product will reach the pinnacle
in 2010 of 10 million total units sold. Originally introduced in 1976, this
proven robust latch has seen record sales and units over the past several
years.
Designed for medium to heavy duty applications, it features a variety of
trip levers and mounting axles for ease of mounting/application and is
available in FMVSS 206 and non-FMVSS 206 versions. Applications are diverse
and vary from personnel doors, compartment/baggage doors, hoods/access
panels, as well as door hold-open applications .
Please visit the TriMark
website for additional information.
|
|
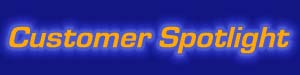
|
|
Antonio Cokovski
Antonio currently serves as Director of Engineering for Wheeled Coach where
he is responsible for product development, design, documentation and print
control for all company products. This includes the scheduling of
engineering projects so as to best utilize available personnel. He also
supervises the process of communicating customer specifications to the
operations group at Wheeled Coach.
Antonio is a mechanical and industrial engineering and management graduate
of St.Cyril and Methodias University in Macedonia – Europe. He has also
earned professional certification as a Quality Manager, Quality Auditor,
Master Six Sigma Black Belt Elective, Lean Leadership, ASQ Judge for the
Word Quality Conference, and DFSS – Design for Six Sigma and VOC – Voice of
the customer. In addition, Antonio has presented and participated in
multiple seminars and training sessions focused on developing effective
leadership and management techniques in various settings.
Antonio resides in Winter Springs, FL with his wife of sixteen years, and
two children.
|
|
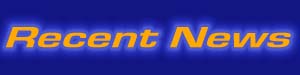
|
|
Mother Nature Throws a "Curve
Ball" at bauma 2010, Munich
Mother Nature, in the form of an erupting volcano and prevailing winds,
conspired to keep exhibitors and visitors away from the bauma Munich 2010
event this year but the overall mood remained positive during the run of
the event.
Companies like TriMark were forced to improvise with personnel and
exhibit displays. None of the personnel fromTriMark China were able
to make the trip which meant that the TriMark Europe and West Alloy
crew had to do yeoman service in making sure that they were there for
customers and friends.
Here are some quick observations from the event:
- Visitor
quality good despite fewer visitors from overseas
- Record
exhibition space and record number of exhibitors
- Over
415,000 visitors from more than 200 countries
According
to Keith Dolbear, Managing Director of TriMark Europe, bauma Munich
marked a turnaround in the international construction machinery industry,
ushering in the hoped-for change in confidence. And this was despite the
ban on air travel which impacted on most of the fair.
"The mood in the industry shows that in Europe the bottom of the cycle
is now behind us. Confidence has returned. Of course, at the start of the
fair, the exhibitors felt the lack of many customers from Asia and America
– but in the second half of bauma, this improved considerably"
according to Ralf Wezel, Secretary-General of CECE, the Committee for
European Construction Equipment.
Although the ban on air travel in Europe prevented visitors and in the end
around 50 exhibitors from overseas from coming to the fair, the mood at the
venue among the approximately 3,150 registered exhibitors from 53 countries
was good by the close of the fair. Already by the mid-way point of the fair
a number of exhibitors were reporting more sales than they had expected after
the difficult last year. A representative survey of exhibitors showed that
bauma Munich 2010 marked a change in mood following a year of crisis in
2009, and that this change is being felt in many international markets.
Because of the turnaround which bauma 2010 has ushered in for the sector
worldwide, there is now additional importance on the already fully booked
bauma China 2010 in Shanghai in November where TriMark China will be
an exhibitor.
TriMark Announces New Sales Representative for Mexico and Latin
America
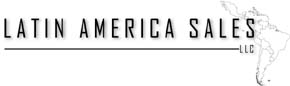
TriMark Corporation is pleased to announce that Matt Haase is the
newest addition to the sales team and will be representing TriMark
in the Latin America/Mexico Regions. "Matt is an excellent addition to
our knowledgeable sales team and we are excited to have his highly capable
representation in the Latin America and Mexico regions," states Patti
Knowlton, TriMark President. "We are truly excited to have Matt
on board and working with TriMark customers in that part of the
world."
Matt may be contacted at:
Latin America Sales
Matt Haase
(541) 368-7958 Work
(541) 223-8753 Cell
sales@latinamerica-sales.com
Please refer to the Sales
Rep Directory at the TriMark website or click on the Contact
US button at www.trimarkcorp.com
to locate the TriMark technical representative in your area.
|
|
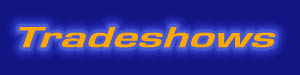
|
|
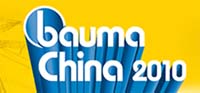
Bauma
China 2010
November 23-26, 2010
Shanghai, China
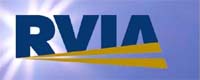
National
RV Trade Show (RVIA)
November 30-December 3, 2010
Louisville, KY
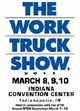
Work
Truck Show
March 8, 9, 10, 2011
Indiana Convention Center
Indianapolis, IN
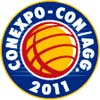
Con
Expo 2011
March 22-26, 2011
Las Vegas Convention Center
Las Vegas, Nevada
|
|
|
|
EDITOR'S NOTE: If you would like to send a
copy of this e-newsletter to a friend, colleague or associate, the Send
to a Friend link at the bottom of this newsletter is a convenient
method for providing them with their own personal copy.
|
|
|
Global Capabilities and Increasingly
Positive Economics
|
|
I hope all of you are enjoying your summer so far. It's hard
to believe that the Fourth of July has come and gone and we are looking at
Labor Day being close on the horizon.
This issue's letter is going to be longer than normal because I want to
share with you more detail on our current supply and demand issues. In past
issues of the newsletter I've reported that we have been struggling with
getting the company back "in sync" with the dynamics of most of
our markets. At the risk of sounding a bit like a broken record, I want to share
with you that we continue to be challenged with production lead-time issues
as well as late deliveries which are more times than not, a direct result
of the lead-time issues. Improved market conditions have exceeded
expectations (better than the line going the other direction) and are
causing issues up and down the total supply chain. Inventories have been
depleted and because no one is carrying extra inventory, meeting the
unplanned increase in demand is causing delivery issues across the supply
and demand spectrum.
For example, Class 8 truck orders were up 93% in June 2010 as compared with
June 2009 which means that we need to be able to supply the increase in
demand. In "normal" market times we would be able to supply many
of these parts from inventory that has been built up. In the current market
environment, our focus is just keeping up with the demand for products
needed today with no time left to replenish the inventory.
I can assure you that everyone at TriMark is focused on resolving
these issues and moving forward. I can share with you that we've actually
had situations where a TriMark employee has driven to a customer
location to make sure parts are delivered when needed. All we can ask from
our great customers, new and old, is that you bear with us and assist us as
much as possible with projections on orders so that we can attempt to get
ahead of the curve. I just can't stress enough how much of an impact this
makes for us in Production and Inventory Control and the delivery of
orders.
Steve Dahl, TriMark's Vice President of Manufacturing, asked me to
share with you the actions TriMark is taking to deal with current
and future demand. TriMark is:
- Working
to understand current and future customer demand in this new economy
- Goal
is to have an accurate 12 month rolling forecast from our customers
- Expediting
materials on a daily and weekly basis as needed
-
Adding new
suppliers to our supplier base for alternative resources when current
suppliers cannot respond to the requirements
- Exercising
conformance to TriMark's Supplier Development program
regarding: Quality, Delivery and Price
- Working
overtime in the manufacturing and support departments as needed
- Adding
personnel / resources throughout TriMark to meet workloads and
demand
I also want to let you know that we are
presently taking a very close look at some current dynamics taking place
with raw materials. We are seeing some preliminary indications that
availability and pricing on materials such as stainless steel may be an
issue but we don't have enough information for a complete evaluation at
this point. I will plan to give you a full report in the next issue of this
newsletter.
TrMark is absolutely committed to getting ahead of this issue and
your continuing support really does motivate us from the standpoint of not
wanting to risk disappointing our customers. Thanks again for your
business.
Patti Knowlton
General Manager
|
|
Wheeled Coach Success – A Story of Trust
|
|
This is a story of how one TriMark customer
moved from being just a customer to becoming a true fan. This is a story of
why relationships are such a critical component of successful business
partnerships. This is a story of how exceeding expectations creates an
environment for future growth. This is a story of trust.
Wheeled Coach
Industries (www.wheeledcoach.com),
the largest single brand manufacturer of ambulances in North America, is
located in Winter Park, Florida. The Wheeled Coach core business consists
of custom built T-I, T-II, T-III, and Medical Attack Vehicles, as well as
light, medium and heavy-duty rescue units and law enforcement specialty
units.
Wheeled Coach is focused on delivering customers the best possible value
while meeting their "specific" vehicle needs. Wheeled Coach
enjoys a justly-deserved reputation as the leader in product innovation and
technological advancements.
Wheeled Coach states
that their products stand apart from competitors based upon:
- State-of-the-art
customized manufacturing
- Superior
engineering capabilities, including a full Pro/ENGINEER software
implementation
- Full
product line that meets or exceeds federal specifications
- Most
are custom designed and engineered to unique customer specifications
The Predicament
Wheeled Coach contacted TriMark after frequent field failures of
their prior door hardware as well as pressure from end customers to provide
a door system alternative. The functionality and reliability of the old
product was not good and the customer base was very dissatisfied. Antonio Cokovski,
Wheeled Coach Director of Engineering states, "The relationship just
was not working for us or our customers."
At that time, the Quality Control Manager at Wheeled Coach was familiar
with TriMark and the company's reputation for problem-solving and he
was the one who initiated the contact and drove the initial program.
The Solution
Wheeled Coach's
goals and objectives were to have TriMark create a floating system
that would fit all door sizes, minimize installation time and solve
installation issues that they currently had with their existing supplier.
Working with Cokovski and his team, TriMark engineered a newly
styled handle (020-1100) specific to Wheeled Coach which incorporated the
floating function (when locked) for the entrance and compartment door
systems. TriMark also created a new handle for the trailing door
which was designed for easy access to the door opening mechanism, ease of
operation as well as being an excellent ergonomic fit. According to
Antonio, TriMark came in and worked directly with engineering,
purchasing and sales to provide a quality door system that is functional
and reliable.
"I chose the TriMark team to work with, because from the
beginning of our relationship, I developed high level of trust towards you
and your team as well. I believed then and I believe now that Wheeled Coach
and TriMark have enough smart people to bring this project to big
success for both companies," states Cokovski.
"I also had a very clear set of expectations about what the new design
should be (floating handle, automotive style, fully functional, etc,) and
the TriMark team showed us they were up to the task from the
beginning. We had weekly meetings and I really liked TriMark's team
approach, including their professionalism, attitude and behavior. They
approached ideas with an open mind and made the ideas happen."
Cokovski continues.
"There were some critical areas where TriMark really exceeded
our expectations," states Wheeled Coach. Examples include project
schedule, cost savings, assembly savings, weight savings, new
functionality, quality improvements, aesthetics, standardization of
product, keyed alike vehicle, keyless entry and others."
Safety
Safety is paramount at Wheeled Coach - from product design through
manufacturing - and is verified with real world testing. Recently Wheeled
Coach subjected a complete ambulance fitted with TriMark products to
a voluntary side impact crash test as a testimony for compliance to current
and future safety standards. The structural integrity and occupant crash
protection was assured as well as the performance of the TriMark
door hardware system. The door system meets all Canadian crash test
standards and is also a NHTSA (National Highway Traffic Safety Association)
approved design.
TriMark was also responsible for a parallel project which was taking
place involving the design and manufacture of an emergency door release
which is unique to Wheeled Coach. Wheeled Coach SafePASS™ – Patient Access
Safety System is a direct override system allowing for emergency exit from
a vehicle. Designed specifically with a crew and patient safety in mind,
this locking system provides improved ergonomics and protection. The
exterior door handles have large, deep wells for a firm grip even with
heavy gloves. The unique TriMark floating mechanism helps eliminate
wear and tear normally caused by trying to open a locked door. And, the
emergency "direct release" tabs allow for doors to be opened in
the event an accident has bent the door lock control rod. Other locking
mechanisms can jam, making patient unloading and crew exit difficult and
possibly dangerous.
When we asked Antonio to sum up his experience to date with TriMark,
this is what he told us. "I can trust them. I can sleep at night
because TriMark is my hardware supplier. If a company chooses TriMark,
they will be very satisfied with their product and relationship.
Would You Like to Have Your Company Featured in a Future TriMark
Newsletter?
If the answer is "yes", then we should talk! In future issues we
would like to feature some of our customers (one per issue) and talk about
how they use TriMark products. If you would like your company to be
considered, then please contact TriMark at tips@trimarkcorp.com.
|
|
Rotary Latches – Building TriMark's
Reputation One Latch at a Time
|
|
How many times have you heard the term
"market leader" and really wondered if it was all just hype. Is
it just to get you to pay attention to the product being promoted only to
find out that it's merely an average product? If your answer is
"yes" don't feel alone as we've all been lead down that path at
some point.
When we tell you that TriMark is the "market
leader" in rotary
latches, you won't need to dig too deeply before you realize that this
is more than just hollow hype. TriMark's rotary latch experience
dates back over 30 years and during that period of time TriMark has
been recognized as a real product innovator with multiple patents as well
as many unique and exclusive features. We like to say that TriMark
rotary latches are "Often Copied but Never Equaled."
TriMark offers the widest range of rotary latches and leads the
industry in reliability and durability. Products range from basic
stand-alone designs to integrated linkages for both FMVSS 206 and non-206
applications. Offering a broad selection of rotary latch sizes, versions, features
and options to meet virtually any application, all TriMark rotary
latches feature the highest levels of quality, security and strength. In
addition, all TriMark rotary latch products are covered by TriMark's
comprehensive worldwide warranty, giving you confidence and peace of mind.
TriMark has sold over 20 million rotary latches and is currently
producing about 1.5 million units per year for a variety of customers and
industries in the non-automotive vehicle markets. Applications include
personnel doors, compartment/baggage doors, as well as hoods/access panels.
The product range covers light duty up to heavy-duty platforms and
versions. Rotary latches are produced as stand-alone products as well as
being integrated into other finished products such as paddle handles and
door modules. Integration of electronics is also available providing power
locking, power release and door open sensing providing a complete
mechatronic solution.
In addition, accessories such as striker bolts, cage nuts, rods and clips
are available to provide a comprehensive access solution.
More about Federal Motor Vehicle Safety Standard (FMVSS) No. 206
This safety standard covers door locks and door retention components in
passenger cars, multipurpose passenger vehicles, and trucks.
The safety standard requires locking systems and specifies load
requirements for door latches and door hinge forces encountered in a
vehicle impact. The design and testing requirements of the FMVSS 206 safety
standard require a primary and secondary latching position and must
withstand transverse and longitudinal load forces and inertial forces
without opening. In addition, a complete door system analysis of ALL
components of the door locks and door retention components for inertia and
inside locking requirements must be performed by TriMark or the
vehicle manufacturer.
A majority of TriMark products comply with FMVSS 206 and are
identified in TriMark's website, catalog and technical publications.
These products have been thoroughly tested in accordance with SAE J839 for
the load requirements.
For more information, please select from the following links to TriMark's
Rotary Latches:
In the following issues of the newsletter
we will take a closer look at several of TriMark's Rotary Latches.
|
|
TriMark Participated in Prominent
Armored Vehicle Show
|
|
TriMark recently participated in
one of the country's premier military shows.
TriMark is a designer and fully-integrated manufacturer of door
hardware systems for heavy duty vehicles. The Armored Vehicle Hardware
Systems group specializes in designing and manufacturing custom door
hardware modules that reduce purchased part counts, reduce vehicle assembly
time, reduce weight, reduce lead times, and reduce OEM engineering time
while improving overall field performance. TriMark draws on over 35
years of heavy duty hardware experience, along with MRAP, MTVR, MMPV
production and JTLV development work to help OEM's with light weight,
up-armored, and power-assist door module designs. Simplify with TriMark:
One Piece…One Supplier…Infinite Solutions.
The show was the IDGA
Military Vehicles Exhibition and Conference, which was held August 11 – 12.
It is the largest stand-alone military vehicles exhibition in the US.
Displays included the latest vehicles (wheeled and tracked), components,
and after-market products in the light, medium, and heavy-duty categories.
Highlights included:
- Service
solutions including vehicle life-cycle management, maintenance, and
logistics in support of vehicle deployment and longevity
- Personnel
involved in the important programs including LAV, Stryker, M-ATV,
MRAP, AAV, Abrams, Bradley, and HMMWV
- Program
updates, educational sessions, and practical hands-on demonstrations
in the show floor theatre
- Insights
from the nation's most advanced technology think-tanks, including labs
and academia, covering ballistics, armor, communications, and other
next-
Multiple platforms, programs, services,
DoD, international partners, vendors, and academia came together to
network, talk shop, and discuss how to best meet the needs of our
Warfighter's next-generation advancements.
While final numbers have not been released for the 2010 conference, the
2009 Military Vehicles Exhibition & Conference had over 3,500 attendees
and 200 exhibitors who raved about the networking, connections, and lessons
learned.
|
|
|
|
TriMark Corporation
500 Bailey Avenue
PO Box 350
New Hampton, IA 50659
Toll Free: 1-800-447-0343
Phone: 1-641-394-3188
Fax: 1-641-394-2392
Email: tips@trimarkcorp.com
Visit us on the web at www.trimarkcorp.com
This e-newsletter is a service of TriMark Corp. and
is produced by The
Bearings Group
|
|
|