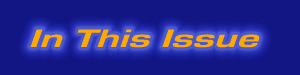
|
|
Click
Here for Printable Version
Click
Here to View as Web Page
Quick Content Links
|
|

|
|






|
|
|
|
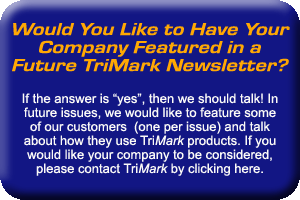
|
|
TriMark History in Logos
|
|
As TriMark has
grown and changed, the logo that represents the TriMark brand has
evolved with the times.
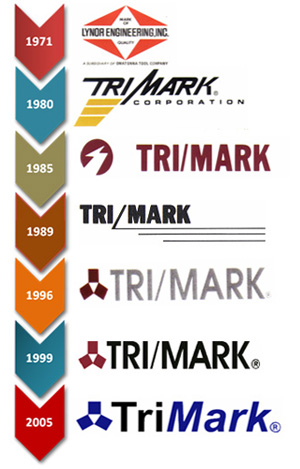
|
|
Special Products for Special Vehicles
|
|
In
addition to TriMark Service and Replacement Parts providing original
hardware products and keys to RV dealers, locksmiths, and various
end-users, TriMark has also been involved with providing
"Access Solutions" for some highly visible and recognizable
specialty vehicles.
Do you recognize these marketing icons?
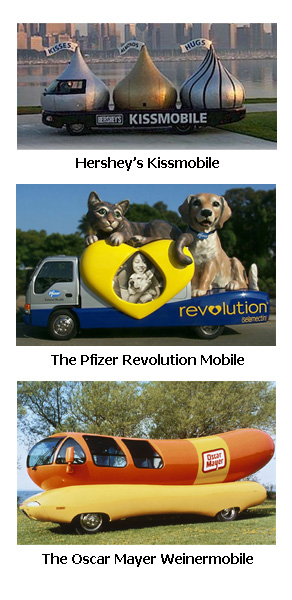
TriMark's 40 Year Presence at Top
Industry Tradeshows
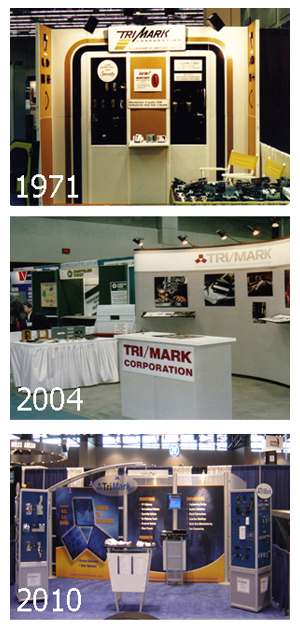
|
|
TriMark "Access
Solutions" Stand the Test of Time
|
|
For
anyone who does not believe that good product design can endure and even be
improved upon, they just need to take a closer look at some of TriMark's
legacy products which are the "grandfathers" of many of today's
successful systems and products.
The 718 Series Two Rotor Latch was originally developed in 1975, was the
foundation for our popular 050-0100 Two Rotor Latch. Over 10 million units
sold, this proven robust latch fits a wide range of applications and
markets. The 2000 Series Elixir Door Latch was first introduced in 1978 and
is still sold today as a 060-0251 Trailer Latch. This product was one of
the first to have an integrated plunger latch in a paddle. The photo below
is one of the first prototypes that were hand crafted, tested and marketed.
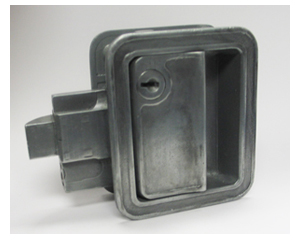
The 710S Series Compartment latch is still sold to Caterpillar as a
030-0150 Heavy Duty Compartment Latch, and was the first integrated paddle
and rotary latch. And finally the 731 Series Flush Paddle still lives on as
a 030-0200/0250 Paddle Handle for the demanding needs of forestry and
construction equipment.
TriMark's rotary latch product line (20 million produced and still
counting!), a variety of paddle handles and latches these products have
all helped create and sustain TriMark's reputation for innovative
mechatronic door access systems.
|
|
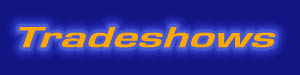
|
|
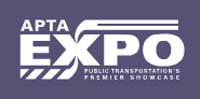
APTA
Expo 2011 (Transportation Show)
October 3-5, 2011
New Orleans, LA.
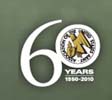
AUSA
Annual Meeting and Exposition (Armored Vehicle)
Oct. 10-12, 2011
Washington Convention Center, Washington, DC
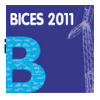
BICES
2011
Oct. 18-21, 2011
Beijing Jiuhua International Exhibition Center
Beijing, China
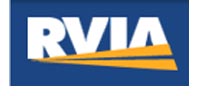
2012
National RV Trade Show
Nov. 29 - Dec 1, 2011
Kentucky Expo Center
Louisville, Kentucky
|
|
|
|
EDITOR'S NOTE: If
you would like to send a copy of this e-newsletter to a friend, colleague
or associate, the Send to a Friend link at the bottom of this
newsletter is a convenient method for providing them with their own
personal copy.

|
|
|
Looking Ahead While Looking Back
|
|
As I was thinking about my message to you for this special
issue of the TriMark e-newsletter celebrating TriMark's 40th
Anniversary, I was suddenly struck by a "reality check" how do
40 years fly by so quickly? While not the first employee, I can tell you
that I am in the "Top Ten" so I've had a very good seat from
which to see TriMark and its predecessor companies grow and change
as the times and our customers have dictated. While hindsight is always
20/20, I can say that as a company we've always tried to do the right thing
for customers and for our employee/owners.
I'm sure you've noticed in your business how quickly the technology changes
as it always seems to be a bit of struggle to keep up with the latest and
greatest. While we were combing the archives for information for this
newsletter, we thought it might be fun to share with you some of the
information we dug out from the "old days." For example, we ran
across a story that Ric Marzolf, VP of Research and Development, wrote for
our internal newsletter back in 2002. He was reflecting on the changes that
had taken place in our Engineering Department during his first 25 years
with the company. We thought it would be fun to include that story for you.
How many of you remember the slide rule?
We also took some time to talk with some of the long-time employees about
the changes they've witnessed during their time at TriMark. In
addition, we dug deep into the archives and found some photos of some very
special and high-visibility product applications (see Special Vehicle
story) TriMark has been involved in through the years.
While we take this time to look back 40 years and reflect on the road we've
taken to this point, we also have to look at our company GPS (there's a
term you didn't hear 40 years ago!) and plot the course for where we want
to go in the future. The TriMark team continues to push forward its
commitment to providing effective access solutions for our global
customers.
While you and I will probably not be around for TriMark's 80th
Anniversary, won't our successors have fun laughing at our
"ancient" technology? Thank you for your continued support of TriMark
nothing happens without our dedicated employees, dependable suppliers and
great customers!
Patti Knowlton
General Manager
|
|
TriMark Celebrates 40 Years of Door and Access
Hardware Innovation
|
|
TriMark,
a global designer and manufacturer of quality hardware products for the
recreational vehicle, agricultural, truck, construction, and industrial
enclosure markets is celebrating its 40th anniversary this year.
In 1971, TriMark Corporation was founded in New Hampton, Iowa with
humble beginnings as a tool and die shop. The original owner had a vision
to automate the die cast and assembly process supporting the window
hardware market. Since then we have grown on the basis of the Midwestern
work ethic, engineering excellence, product quality and a drive to serve
customer's needs with products that fit THEIR requirements, especially when
that meant innovation, problem solving and a customized solution.
In 1975, TriMark developed a heavy duty rotary latch
for Winnebago Industries motor homes and Caterpillar construction
equipment. This product line was the foundation for the popular 050-0100
Two Rotor Latch that is still sold today and was the beginnings of the
current vehicular door hardware product line. TriMark has been
recognized as a real product innovator with multiple patents as well as
many unique and exclusive features. We like to say that TriMark
rotary latches are "Often Copied but Never Equaled."
Today TriMark offers the widest range of rotary
latches and leads the industry in reliability and durability. Products
range from basic stand-alone designs to integrated linkages for both FMVSS
206 (Federal Motor Vehicle Safety Standard for Door Locks and Door
Retention Components) and non-206 applications. Offering a broad selection
of rotary latch sizes, versions, features and options to meet virtually any
application, all TriMark rotary latches feature the highest levels
of quality, security and strength.
In 1989 TriMark employees added the pride of ownership to their
motivation by purchasing the company and becoming 100% employee owned. Over
the years, we've grown from ten employees to more than 300.
Our New Hampton facility is the corporate headquarters and
is sited on twelve acres providing 132,000 square feet of administrative,
engineering, manufacturing, service, and support activities.
In 1997, TriMark Europe was incorporated as a sales, engineering,
distribution and logistics facility supporting the European construction
equipment market. TriMark Europe is located at Bardon Hill,
Coalville, United Kingdom. In 2007, TriMark Europe Ltd, a subsidiary
of TriMark Corporation, has acquired West Alloy Ltd. Located in the
UK. West Alloy is a market leader in the design and manufacture of locks,
hinges, window stays and associated fittings for the world's best-known
industrial and leisure vehicles.
In 1999, TriMark Service and Replacement Parts Division was launched
and is located in a 9,600 square foot facility in New Hampton, Iowa.
Providing the original hardware products and keys to RV dealers,
locksmiths, specialty vehicle users and end users, we support "just-in-time",
repair part packaging and stocking programs. Technical staff can assist in
the proper selection and application of our products and help with the
identification of repair or service parts.
In 2003 TriMark
launched e-ASK electronic Access and Security Keyless-entry
product line consisting of RF transmitter FOBs, keypads, I/O modules, power
lock actuators and a wide variety of accessories for electronic products.
Our keyless access control systems pave the way for innovative technologies
that make non-automotive vehicles more convenient and secure.
One of TriMark's strategic strengths is the ability to provide
complete door systems. Our broad product line includes handles, latches,
strikers, rods and accessories, key cylinders, actuators, ignition
switches, key pads and FOBs, CAN I/O modules, and door kits. And because
today's applications are increasingly integrating mechanical systems with
electronics and computer controls, TriMark has dedicated itself to
being the undisputed leader in mechatronic integration of access systems
for personnel doors, access panels, engine compartments and hoods, interior
compartments, windows, and vehicle controls.
Following the global shift of construction equipment
manufacturing, in 2007 TriMark obtained its license to manufacture and sell
in China under the name TriMark (Xuzhou) Automotive Components Co.
Ltd. in Xuzhou, China. Caterpillar and John Deere are two well known global
customers that are served from TriMark China as well as a host of
domestic customers in the China construction market.
In 2008, TriMark established the Armored Vehicle Business Unit that
is dedicated to serving the needs of key armored vehicle OEM's as well as
the commercial security market. Offering security, reliability and modularity,
the TriGuard line of TriMark's heavy duty latches, linkages, handles
and door modules are specifically developed for heavy duty armored vehicle
applications. These robust door product/systems simplify vehicle and field
attachment with reduced attachment points and door assembly.
Product quality is the primary driver of TriMark
product engineering and its manufacturing processes. The emphasis on high
quality persists throughout a worldwide supply base as suppliers are
selected, not based on price, but the ability to deliver what TriMark
is expected to provide; safety, quality, reliability, value and pride of
ownership. Product validation is handled in TriMark's world class
testing laboratory, which is able to accelerate harsh operating
environments. Salt spray, dust chamber, lifecycle, and strength testing are
performed to validate and further compress the time needed to launch the
entire door system.
Customers soon discover TriMark works even harder after the order is
placed to insure that the logistics of supply remain consistent and
communication open. Customer service representatives are available to
immediately answer questions for clients that experience fluctuations in
their manufacturing.
We are the industry leader in the design, manufacture, and supply of door
latch systems. Our years of experience provide us with a special knowledge
that goes far beyond the simple function of opening and closing a door.
Applications experience encompasses access systems for personnel doors,
access panels, engine compartments and hoods, interior compartments,
windows, and cab and vehicle controls.
TriMark's customers are found in a diverse set of both on-road and
off-road applications such as industrial enclosures, power sports, mass
transit, armored vehicle materials handling, utility truck, fire and
rescue, heavy truck, special purpose vehicles, RV, bus, and motorcoach,
agricultural equipment, and construction equipment. Not surprisingly, many
of the markets are global in nature. And for that reason, TriMark
has not ignored the need to integrate itself into the global marketplace.
Building on 40 Years of Innovation
Together with key factors that characterize the company's
history: innovation, application engineering, product performance,
mechatronics, motivated employees and excellence of sourcing and
manufacturing coupled with a market focus and future global trends will
enable TriMark Corporation to face the future with renewed
confidence and expectation of success.
To share this article with a friend or colleague, please use the Send
to a Friend link at the end of this newsletter.
|
|
Ric Remembers
|
|
Back
in 2002, Ric Marzolf, TriMark's Vice President of Research and Development,
wrote an article for TriNews, TriMark's internal company
newsletter, reflecting on his 25 years with the company. We thought our
readers might find it interesting to see what he had to say at that time
about the changes he experineced during that quarter-of-a-century. In honor
of the 40th Anniversary, he agreed to give us an update on what's changed
since that 2002 article appeared.
TriNews 9/02
2002 is a milestone year for me; I attended my 30th High
school reunion, reached my 25th anniversary at TriMark in August and
recently celebrated 20 years of marriage. The cars I drove and the music I
listened to (still do) are now considered classics. All of this of course
dates my age, but I wanted to reminisce briefly about the changes I have
seen at TriMark's product development going back to the good old
days (kind of sounds like my parents doesn't it?).
Drawings were done in pencil on a drafting table or board hence the term "It's
on the board" (in development) or "back to the drawing
board" (major revisions required). Tools that were used in the
drafting function included drafting machines, scales, compass, templates,
triangles, and electric eraser/erasing shields to correct the mistakes. You
can imagine the time and expense to redraw a drawing or move a detail a
mere .250 in.
Project notes, meeting minutes and a lot of calculations
were hand written on lined paper. Slide rules were used for computations,
including multiplication, division, powers, roots and trigonometric
functions with the first calculators being used in 1975. Mine was a Texas
Instruments TI-1250 and cost $60 for a basic four-function model.
TriMark's Product Development process has gone thru a total of 3
major programs PDG, Flexibility, and the current P3 process plus
continuous improvements and updates for each. Prototypes were crude,
costly, took a long time and were done toward the end of the development
cycle. The tolerances were atrocious and a great deal of fine-tuning was
involved to get them to work the way they should. I have one of the first
Travel Trailer prototypes (Elixir Lock) from 1977 in my office. By
comparison our new Stratasys FDM (Fusion Deposition Modeling) rapid
prototype machine is more akin to a copy machine than the DTM SLS sinter
station machine we previously had and it light years ahead of the rubber
molds and machined prototypes. It will offer us better accuracy, faster build
times and more robust parts. >
> Click here to continue...
To share this article with a friend or colleague, please use the Send
to a Friend link at the end of this newsletter.
|
|
TriMark Employee Memories
|
|
While it may not
be totally unique to a company celebrating 40 years in business, TriMark
enjoys having a relatively large percentage of its employees who can trace
their history with the company back over 30 years. We thought it would be
fun to hear what they have to say about things such as the biggest changes
they've witnessed and some of the other memorable moments that make this
employee-owned company a real family.
When we reached out to about 30 TriMark employees
who've been with the company 30+ years, we weren't really sure just what
information we would get back in response to our questions. Here are a few
highlights we thought you might enjoy. We have not included the names to
protect the innocent!
Question: What is the most significant change in the company that you
can remember?
Most of those who answered this question mentioned the increased use of
technology computers and automation - throughout all company operations.
"When we decided to replace our first computer with an
AS400 we went from a computer the size of a chest freezer to one the size
of a dehumidifier. Of course the machine was more money and I can still
remember Scott Perkins coming in to see it and asking me where the rest of
it was."
Also, the 1989 Employee Stock Ownership Plan, which accompanied the buy-back
of the company, was very high on most respondents list. This answer also
was listed by several respondents when asked about their most memorable
moment at TriMark.
The following was written for a capabilities brochure in 1990 as the
kick-off to becoming Employee Owned
.
A strong work ethic has long been a valuable asset for businesses that
locate in the nation's heartland. At TriMark, it's taken for granted.
Our employees, some 115 strong, represent average work tenure of over 10
years. Yet even with all this experience, we're a young company with an
average age of only 35 years. When you take these employee's
characteristics and consider these employees actually own the company, it's
not difficult to understand why a commitment to quality and service are
taken very seriously. Our pride runs deep. And it shows in our products.
Because we're an employee-owned company we think it's critical to do things
right the first time every time! Should we ever fail to meet the
expectations of our customers, you can be assured we will make it right. We
have more than our jobs on the line here we have our word. And in New
Hampton, Iowa, a person's word isn't just a hollow statement, it's a pledge
and we stand behind it every single one of us.
Today, after 22 years of ESOP, we've grown to 267 employees in the ESOP
and have average work tenure of 12 years with an average age of 44. So we
have matured a little and are proud that we have 30 employees with over 30
years experience that are still delivering on the promises that have
propelled TriMark to where we are today. Today we are welcoming new
employees that have the kind of skills and training demanded companies such
as TriMark who operate on a global stage. We welcome these new
additions to the TriMark family and look forward to seeing them
continue on the successful path that has provided TriMark the keys
to success for our first 40 years.
The addition of TriMark Europe and TriMark China was also
mentioned.
Question: How would you describe your experiences at TriMark?
We'll use this direct statement to speak for a majority of the respondents:
"Well, I love what I do and I guess when you can still wake up and
look forward to going to work, that's a good thing."
Question: Do you have any other comments you would like to share?
"Thirty-five years ago, I was on my way to Waterloo, Iowa to look for
a job. I was going past TriMark and though I would stop. I had an
application in already. Jim Grove, then the supervisor of Die Cast talked
to me and said, "A guy quit in Die Cast this morning, you can start
Sunday night on third shift." I thought well I can do this till I find
something better. Well I'm still here
"
And finally.
"I have never met someone from outside of TriMark who didn't
want to come back and do work for us again. There is something about this
place and the people that instill a lasting positive impression on
people."
Thank you TriMark employees for 40 years of loyal and dedicated
service.
To share this article with a friend or colleague, please use the Send
to a Friend link at the end of this newsletter.
|
|
|
|
TriMark Corporation
500 Bailey Avenue
PO Box 350
New Hampton, IA 50659
Tollfree: 1-800-447-0343
Phone: 1-641-394-3188
Fax: 1-641-394-2392
Email: tips@trimarkcorp.com
Visit us on the web at www.trimarkcorp.com
This e-newsletter
is a service of TriMark Corp. and is produced by The Bearings Group
|
|
|