|
|







|
|
|
|
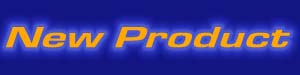
050-1100 6mm Single Rotor Latch
This new automotive style single rotor latch is designed for
medium to heavy-duty applications for on or off-highway compartments and
access panels. It features a modular case design that provides for multiple
latch actuation direction and locations for application flexibility. Other
product details include:
- Compact
size and shape allows for maximum use of door space and minimizes
visibility issues
- Dual
position rotary latching function provides for vertical clearance of
strike for door sag, misalignment and ease of installation
- Use
with 6mm diameter striker loop
System kits
are available and include handles, latches and accessories to provide a
comprehensive access solution.
060-1300 Flush Mount Security Lock
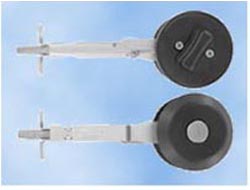
This new product is a redesign of our 060-0300 Flush Mount Security Lock
for Recreational Vehicle entrance doors including Motor Homes and Travel
Trailers. Providing additional security in a remote mounted lock, it
features true deadbolt functioning and is adaptable to power lock
actuation. Other product details include:
- The
KeyOne Plus locking system allows the operation of multiple onboard
locking hardware with a single key or the option to key differently
- Easy
to install, the universal design is non-handed and the gasket is
pre-applied.
System kits
are available and include handles, latches and accessories to provide a
comprehensive access solution.
For
more information go to www.trimarkcorp.com/en/productnew.aspx.
|
|
|
|
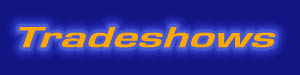
TriMark Corporation's 2009 and 2010 tradeshow
schedule is listed below. Please plan on visiting our exhibit booth if you
are attending any of the following events.
The 47th Annual National RV Trade Show
will be held December 1 ?3, 2009 at the Kentucky Expo Center in
Louisville, KY.
With the recent success of The Work Truck Show )0 2009,
including a 19% increase in attendance from the year before (the second
highest attendance in the show's history!), The Work Truck Show 2010
promises to be a Don't Miss event!
|
|
National Truck Equipment Association Work
Truck Show is a Big Success
|
|
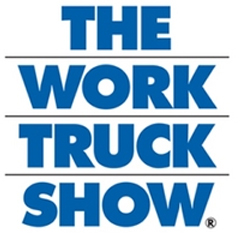
By any measure, the 45th Annual NTEA Convention and The Work Truck Show
2009 held in Chicago during the first week in March was a huge success.
Surely, no trade show's success should be based on attendance alone. But
the crowd of 8,450 was outstanding given current economic conditions. It
was the second highest turnout recorded at a Work Truck Show (the largest
of more than 9,100 was in Indianapolis in 2007).
The mood of the show was buoyant and positive. There was a buzz in the
hallways, restaurants, seminars and people were anxious to talk about how
and when business will improve. By and large, exhibitors reported having a
great show. They were pleased (and to some extent surprised) with booth
traffic. Many exhibitors commented on the quality of the visitors as well.
Speaking of exhibitors, the show was a sellout with 492 companies,
including TriMark, using every square foot (more than 500,000square
feet) of exhibit space, many of them displaying new product offerings.
Adding to the usual truck equipment industry offerings, the Green Truck
Pavilion was the center of green technologies that are available today and
will power work trucks for future generations.
Dave Root is TriMark's Account Manager for Specialty Vehicle Markets
and his observations were consistent with many of the exhibitors and
attendees. "We saw some very positive things come from the show in
terms of new programs being presented by manufacturers. While there is
obvious pressure on pricing, we had a tremendous amount of interest shown
in one of TriMark's feature products ?the application of
electronics to the mix of available truck body features. The convenience of
being able to use a single controller to lock/unlock all of the truck body
access points, as well as the security benefit, generated some very
positive feedback. Electronics is a big growth area."
|
|
Account Manager Update
|
|
TriMark is pleased to announce the following change
to our Account Management team:
Tom Neessen started work at TriMark earlier this year as the Account
Manager for the Ag and Off Road Markets and he was recently promoted to
Global Account Manager. His responsibilities include the continuation of
managing the Ag and Off Road markets as well as leading the effort in
strengthening TriMark's presence in large Global Accounts. Tom is a
native of Cedar Falls, Iowa and attended the University of Northern Iowa.
He brings to TriMark extensive experience (20+ years) in the
precision factory automation and stampings industry with DT Industries and
Doerfer Companies and is familiar with many of our customers in the Ag and
Construction industries. His positions have included National Accounts
Manager, Sales Manager, New Business Manager and Large Engineering Program
Manager.
His accomplishments include:
- Responsible
for development/ restructuring sales organization - direct sale people
and hiring a representative network totaling 15 professionals
- Managing
the sales effort in new business development in specific markets and
accounts
- Developed
detailed plans to execute on all sales and marketing strategies for
the organization
- Effectively
implemented new sales and business strategies for National and Global
Accounts.
Please join us in welcoming Tom to the TriMark
Sales Team
|
|
|
|
EDITOR'S NOTE: If you would like to send a
copy of this e-newsletter to a friend, colleague or associate, the Send
to a Friend link at the bottom of this newsletter is a convenient
method for providing them with their own personal copy.
|
|
|
TriMark Future Remains Strong -
Update
|
|
Is there a light at the end of the tunnel?
Well, we are starting to see a flicker but the tunnel is still one that is
long and there may be some unanticipated twists and turns along the way. I
shared with you in the last issue of the newsletter that we were issuing a
cautious note of optimism and that observation has not changed. We continue
to see increased activity in our core business sectors from current
customers as well as new customers who recognize TriMark as a
potential long-term partner.
One area we use as a sort of barometer is our project portfolio. If TriMark
engineers are busy with the development of customer access solutions and
products then it tends to bode well for additional manufacturing activity.
From Product Engineering to product validation to the tool room, TriMark
is extremely busy right now, so we see this as a positive signal but one we
still view with caution.
One area which has seen no real decline in activity during this economic
downturn is TriMark's Service and Replacement division. It's
difficult to put a specific reason on why the business has not seen any
fall off. It has been our observation that perhaps TriMark customers
are using "downtime" to conduct maintenance and service that may
be overdue.
We can never say enough how much we appreciate our good and loyal
customers. Without your continued support and trust TriMark's future
would not be nearly as bright as it is today. Thank you for your continued
business and support.
Patti Knowlton
General Manager
|
|
New Product Development - Worldwide
Collaboration
|
|
Earthmoving Hydraulic Excavators are very popular in China
and the market for this equipment is growing quickly with many OEM's
developing their own brand for market. When TriMark was first
established in China it was fast revealed that a cab door handle suited
especially for hydraulic excavator equipment was critical to long term
success. Engineering teams in the U.S. and Europe were too busy to take on
another development project and time was of the essence.
Local engineering talent was recruited for TriMark China to undertake
the project. Wang Jing (Design Engineer), under the direction of Yang
Weimin (Director of Technology), were assigned to design the product using
a combination of features from other proven TriMark products along
with some innovative ideas to reduce part count and manufacturing cost.
Miss Wang took responsibility of the project from the very beginning and
has added a great deal of value to TriMark in the process.
Her talents as an engineer were tested in developing a product that would
fit in current applications without modification. Miss Wang diligently went
to work studying the features of TriMark products and in the process
learned the methods and practices of Engineering Changes in a global
organization.
TriMark also wanted to incorporate design features that were shared
with other products and proven to add strength and reliability. Using
Pro/ENGINEER?and Windchill?the TriMark China engineering team
worked with the engineers in the U.S. to review designs, exchange inputs
and advice, and review features that would make the 030-2300 Excavator
Paddle Handle a World Class product. Learning how to work within Windchill? and a totally new work culture proved to be an exciting byproduct of the
collaborative engineering process.
Yang Weimin, TMX Director of Technology commented on the
development project "The support I received from the US engineering
teams are HUGE; the project team, product team, test team, R&D team,
machine/assembly department, purchasing team, PIC?I appreciate that they
helped me with everything without question."
There has been outstanding personal growth in TriMark's China
engineering team as well. Miss Wang is now involved in application
engineering for customers, working with corporate engineers in managing
engineering changes and providing suppliers engineering input on products
in development.
The 030-2300 is the result of the joint TriMark teamwork in both
engineering design and learning the challenges and rewards of working on a
team that is spread around the world. Tooling for this product is nearly
complete and production is expected to begin within the next several months
with several interested OEMs.
It is expected that this will be the first of many new projects that will
utilize simultaneous engineering and global collaboration to allow TriMark
to design faster, while maximizing innovation and quality and to ultimately
create exceptional products for the benefit of its global customers.
|
|
TriMark continuously strives for
Excellence and to exceed Customer Satisfaction
|
|
At TriMark, one of the key reasons
we continue to experience a high level of positive customer relationship
feedback is because we always strive to meet and exceed a customer's
requirements regarding supplier quality. We really do put our reputation on
the line every time an order is placed for one of our high-quality
products.
TriMark's USA facility has been ISO 9001:2000 Certified since 1995.
However, in March of 2009 TriMark became ISO/TS 16949:2002 (with
product design). Our United Kingdom facility has been ISO 9001:2000
Certified for warehouse, sales and distribution since 1995. In January of
2009 the UK facility became ISO 9001:2000 Certified for manufacturing and
assembly of plastic injection molded products. In addition, this facility
is certified per ISO 14001:2004 for Environmental Management.
In December of 2008 we were notified that both the TriMark
USA and United Kingdom facilities achieved Caterpillar Supplier Excellence Process
Certification for MQ1105 Standard-Bronze Level. Click
here to view Caterpillar notification.
|
|
TriMark's Armored Vehicle Hardware
Systems Division Continues to Gain Momentum
|
|
Since the last issue of this newsletter,
TriMark's Armored
Vehicle Hardware Systems Division has been very busy recently
participating in two large military industry events with the goal of
increasing the awareness and relevance of the TriMark brand in this
key market.
At the AUSA (Association of the United States Army) 2009
Winter Symposium and Exposition in February, TriMark introduced its
latest innovationthe COMMANDoor power assisted door module with a
fully functional demonstration door. The COMMANDoor fully integrates
mechanical blast locks and a primary FMVSS latch with a power-assist
actuation system that is controlled with a single, easy to operate, control
handle.
TriMark's Kevin Roths states, "We had a very good exposition
and the COMMANDoor product was a real hit. We had the opportunity to
speak with all of the prime contractors for armored vehicles, and without
exception, their business development, program management and engineering
personnel were impressed with the COMMANDoor's simple and safe
function, full integration and ease of use. With input from this highly
qualified audience, we were able speak to the product's flexibility and the
many customizable options available to fit the unique needs of each
individual vehicle."
TriMark also participated in the IDGA (Institute for
Defense and Government Advancement) 2nd Annual Tactical Vehicles Summit
this past April. This event focuses on the challenges ahead for the MRAP
and JLTV, including testing needs and future development. The IDGA is an
independent entity that caters to all branches of the military and
therefore attracts a real cross-section of attendees to its events. As a
key sponsor of the event, TriMark had unrestricted and exclusive
access to the entire list of speakers--many of whom were high ranking
military personnel.
Kevin Roths reports, "We had the COMMANDoor demonstrator on
display at this event, too, and once again, there was a great deal of
interest in the product and a desire to have vehicle specific application
follow-up discussions. Both military and prime contractor personnel were
impressed with the operation and simplicity of the COMMANDoor, so we
strongly believe this product has a bright future in filling the military's
need to simply and safely open and close heavily armored vehicle doors and
ramps on any grade or terrain."
|
|
5S ?One Component of Lean
|
|
In earlier issues of this newsletter we've discussed TriMark's
commitment to Continuous Improvement and how we as a company embarked on
our Lean journey back in 2007. This journey has paid many dividends for
both TriMark and the customers we serve. In this issue of the
newsletter we would like to give you a closer look at one of the key
components of Lean ?5S.
TriMark's Lean Steering Committee (LSC) was formed with a focus on
laying the foundation of Lean at TriMark. The foundation consists of
a 5S System, Visual Factory Management, and Value Stream Mapping. Let's
take a closer look at what the 5S component is and how it contributes to an
overall Lean approach.
What is 5S?
We consider 5S and Visual Controls to be the organizational tools that
provide the necessary groundwork for workplace improvement as well as
laying the foundation for Lean Manufacturing systems. The 5S discipline
requires clearing out things which are not needed in order to make it
easier and faster to obtain the tools, parts and information that are
needed.
Companies that practice 5S cite the following benefits:
- Reduced
inventory
- Reduced
machine downtime
- Office
and plant space made available
- Improved
productivity
- Improved
morale
- Increased
levels of product quality
- Improved
delivery
- Improved
safety
The key targets of 5S are workplace morale and efficiency. The concept of
5S is that by assigning everything a location, time is not wasted by
looking for things. Additionally, it is quickly obvious when something is
missing from its designated location. 5S advocates believe that the
benefits of this methodology come from deciding what should be kept, where
it should be kept, and how it should be stored. This decision making
process should lead to a dialog which can build a clear understanding
between employees of how work should be done. It also instills ownership of
the process in each employee. As a result, it is often executed in tandem
with standard work which standardizes the processes in which the items
organized in 5S are used.
What Are the 5Ss?
The 5Ss are Sort, Set in Order, Shine, Standardize and Sustain.
Click
here to take a closer look at each.
|
|
Survey Response and a New Question
|
|
In the last
issue of this newsletter (February 2009) we asked the following question:
"We've all been living and breathing the "stimulus" package
for the past 30 days, and with its signing earlier this week, we'll start
to see some of the funds starting to flow. Do you think the
"stimulus" package contains enough of an immediate focus on business
and the challenges they face in maintaining or creating new jobs?
The verdict is in and 66% of respondents answered a resounding
"No" to that question.
It's now been approximately 3 months since we asked that last question so
keeping to the same general theme, we invite you to answer this question:
|
|
|
|
This e-newsletter is a service of TriMark
Corp. and is produced by The
Bearings Group
|
|
|